“I had a stereotype about what manufacturing would be like - dusty, [with] managers who weren’t interested in HR. But I was surprised. I’ve had highly engaged workforces in clean environments,” says Adam Goldman who practised HR in manufacturing spaces for 15 years and had to re-evaluate his assumptions about the manufacturing work.
Manufacturing jobs may surprise those who hold preconceived assumptions about the industry, just as they surprised Goldman. The biggest discovery may be that experts endorse a spell in manufacturing as a solid career development opportunity.
HR in manufacturing greatly differs from HR in a workplace. So before you jump in, consider some of the main differences—and most pressing HR challenges in the manufacturing industry—you'll be dealing with.
7 HR Challenges in the Manufacturing Industry - With Solutions
1. Coping up with the talent shortage & hiring right
Recruiters are finding it tough to attract skilled manpower due to various HR challenges in the manufacturing industry. The manufacturing industry 'appears' unattractive to many people. Prospective younger employees see manufacturing as "boring, old, and not creative," according to Seema Pajula, Vice Chairman (US Industries) and Insights Leader for Deloitte.
The talent shortage is predominant simply because of the above HR-related stereotypical perceptions. These particular perceptions about manufacturing hide the actual industry advancements. And in terms of ‘brand’ and job openings, manufacturing may be lagging behind retail and tech firms.
Furthermore, with the inability to identify and hire sufficiently skilled individuals who do not require substantial amounts of training and education to just get started, manufacturing HR departments must actively endeavour to fix the manpower problem.
All this has created a disconnect between expectations v/s reality regarding job stability, career advancement, salary, and benefits. The necessity for a specific skill set required by the employee makes the challenge of filling many openings even more difficult.
The Solution:
Manufacturing is certainly in need of a rebranding to promote its innovative technologies and prospects for career progression. This will almost certainly entail adopting practices that promote a more employee-centric workplace where flexibility is widespread.
Several manufacturing companies partner with digital HR service providers to reduce human intervention in hiring activities. These activities include sourcing resumes, allying with colleges and universities, selecting more relevant candidates, or arranging follow-up interviews through AI. With benefits ranging from cost-effectiveness and more diverse talent, AI will make the process transparent and more efficient.
2. Minimizing injuries & common safety incidents
Manufacturing employees are often in danger of industrial accidents because of their work involvement with machines, planers, lathes and other sorts of production tools. Employees who work with hazardous chemicals, for example, maybe exposed to lead in the form of dust or fumes when making batteries.
Falls are also a constant threat in the manufacturing industry. Employees are at risk when working on high platforms, cherry pickers, ladders, or any other elevated area. Even noise from manufacturing machines can harm their hearing if they are exposed to it for an extended period.
The Solution
“Promoting worker safety goes beyond just the safety manual or handbook. It’s really about creating a culture that’s committed to [and] very much focused on safety and accountability. It’s about preventing, reducing, or eliminating the severity or claim before it ultimately happens.” - Brian Kramer, Manufacturing Industry Practice Leader, The Hartford
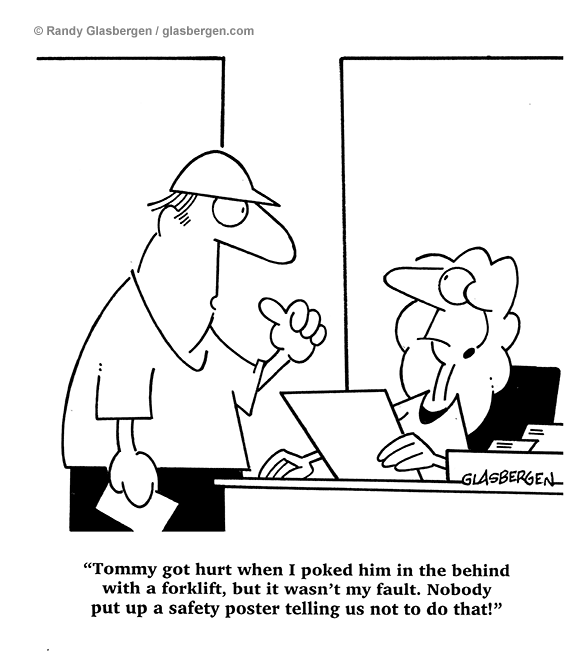
Manufacturers attempting to fill the gaps must prioritise safety and responsibility, as suggested by Kramer. This means HR must guarantee that their companies have implemented health and safety measures. Investing in a scalable and appropriate training program can also help in preventing risks.
Take, for example, the Coca-Cola Bottling Company. The company witnessed a 60% reduction in ergonomic injury rates and a 70% reduction in employees' compensation claim costs after implementing an interactive "boot camp" training programme for workers that included "train-the-trainer" education for onsite supervisors.
3. Breaking the communication barriers
Communicating with employees is among the major HR challenges in the manufacturing industry. For starters, you simply can't send a company-wide e-mail informing employees about their new retirement plan because most manufacturing employees work in the field. This is why HR has more work to do in terms of interacting with employees.
For example, an HR professional discussing various employee-related topics with line employees, such as leave affairs, shift working, hours of work, weekly offs, holidays, and so on, may need to make extra efforts to ensure that the employees understand and follow the rules.
The Solution:
When it comes to contacting employees in the manufacturing sector, traditional internal communications platforms like newsletters, emails, and the intranet aren't necessarily up to the task. You can cut through the clutter and noise of the modern manufacturing environment and reach your staff with important information using a variety of new digital solutions.
Adopting intelligent personal assistance, such as peopleHum’s chatbot Phia, offers guidance that helps employees with their employment-related queries. Notifications are provided with our app on cellphones for employees on the go. They can receive alerts of any company-wide announcements without the hassle of logging into the company server.
4. Dealing with physical and mental overload
Traditional manufacturing employees suffer from the physical and cognitive workload all because of their daily tasks. Tasks related to handling heavy products and repetitive assembly movements contribute to creating the physical workload. Manufacturing employees may also experience difficulties in conducting assembly activities and supervising technologies.
The Solution:
Conduct a benchmarking survey to determine how engaged your staff are. Develop an internal communications strategy based on the outcomes of the survey that you can monitor. Future engagement surveys can be used to evaluate decreased employee turnover or higher safety rates.
peopleHum's people analytics can be used to plan their work shifts better to reduce their physical and cognitive workload due to their operational activities along the production line. Our employee engagement system dedicates a space for the generation of employee ideas related to organisational growth. It eases problem-solving by interconnecting tasks with the organisation’s real-time data.
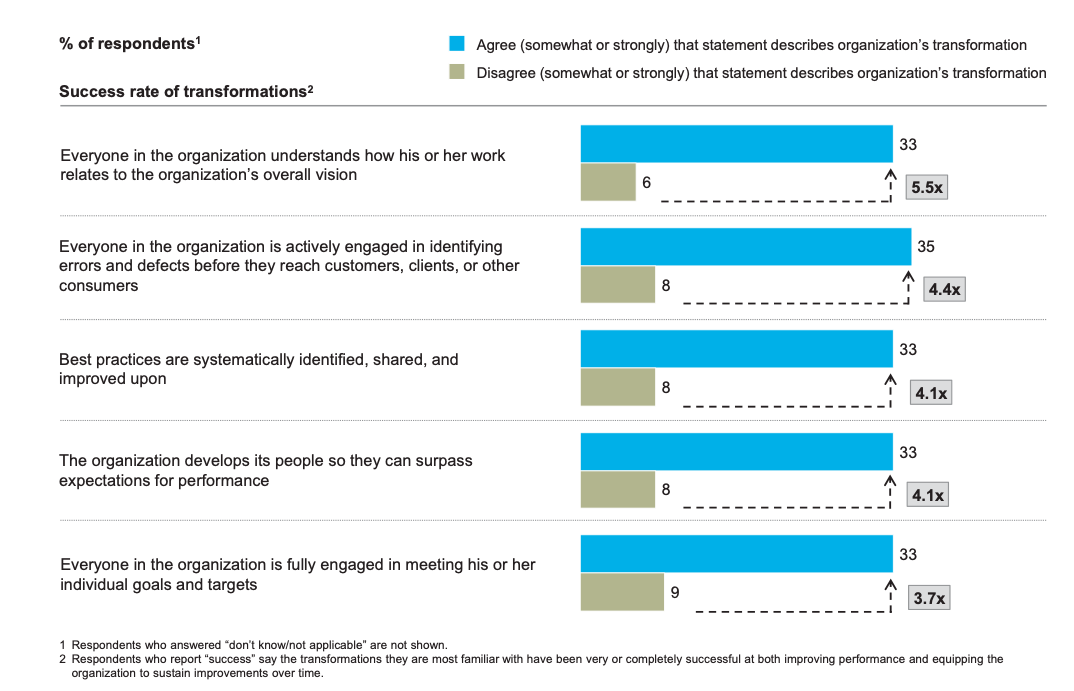
5. Retaining employees
Reports by SHRM shows one of the biggest HR challenges in the manufacturing industry is “saying goodbye to boomers.” A study by Deloitte predicted that around 2.6 billion baby boomers will retire from the manufacturing industry.
When combined with an often insufficient investment in employee growth and development - both professional and personal - as well as the widespread perception of stagnant pay packages, inadequate benefits, and a terrible work environment, battling high turnover rates can be a difficult task. The increasing average age of the manufacturing workforce merely adds to the turnover.
Other reasons for the increase in turnover may be due to no growth or development of the employee on both professional and personal front, low pay package, lack of benefits or poor work environment.
The Solution:
“Any of us can be hit by a bus tomorrow, so cross-training is huge. Transferring knowledge before workers leave is a way “to learn not just what they do but how they do it and why they do it.”— Julie Mann, HR director at Neogen Corp
What we understand from this is that employers must,
- Provide horizontal job opportunities that are less physically demanding to encourage ageing seniors to stay with the organisation
- Dedicate a forum for elders to share their knowledge, experience, and abilities with younger, less experienced workers, such as a mentorship programme
- Encourage your older employees to take advantage of any digital training your firm provides to guarantee they have the skills they will need in the future.
- Strengthen the employer brand to improve the company's ability to recruit and hire top candidates
6. Carrying out performance evaluations
For many years, manufacturing has used flexible levers and performance-management programs to increase productivity and profit margins. They normally had good initial results, but as management became distracted and people returned to their old habits, their gains vanished or diminished.
Strangely, many manufacturing operations don't have real-time performance insight. Rather, they examine key performance indicators (KPIs) on a weekly or even monthly basis. Supervisors are hesitant to discuss and handle issues until they have spiralled out of control without real-time transparency.
For example, because it did not have enough solutions for tracking daily performance, one manufacturing appliance company with an assembly line that produced $4 million in product each month accumulated roughly $1 million in additional backlog over the same period.
The Solution:
The present manufacturing downturn, in which many manufacturing firms are operating at lower capacity, may be a perfect time for industrials to reconsider and experiment with new digital performance-tracking technologies. A performance management system is a dynamic process designed to enhance employee capability and organisational productivity.
It allows detecting those employees performing below standards by comparing their actual performance with the standards. If an employee performs below standard, other HR practices—such as vocational courses—can be provided to train their skills to conduct the tasks.
Simultaneously, an effective performance management system identifies those higher-performing employees suitable for the extra assignment, merit-based compensation, promotion, or leadership development.
7. Making daily adjustments to the nature of work
Lack of regular shift patterns, short notice of scheduled work hours, or last-minute shift changes can negatively impact manufacturing employees. The implications of not having a set work schedule can make work life unpredictable. A constantly fluctuating work schedule is stressful for employees, as well as HR.
For example, in factories that operate day and night shifts, the HR department must take a balanced approach to shift allocation for all three shifts. What tops these HR problems in the manufacturing industry is ensuring minimal absenteeism and reducing overlapping and effective use of both people and machinery.
The Solution
The adoption of workforce management system addresses these specific HR challenges in the manufacturing industry by supporting real-time training, tracking and complex activities, thus reducing human errors. The fact is that managing scheduling in the manufacturing industry is too complicated to handle without automated tools. The risks to your organization’s bottom line is simply high to leave it to chance.
Final Thoughts: Is Your HR Strategy Factory-Ready?
HR in manufacturing is more than paperwork and compliance. It's about building trust, reducing friction, and enabling the workforce to thrive in an environment that is physically demanding and constantly evolving.
To get ahead, manufacturing companies must embrace digitized HR tools, strategic workforce planning, and a culture of continuous improvement.
Want to explore an all-in-one HR platform that fits the manufacturing world?
Book a free demo with peopleHum
FAQs
1. What are the top HR challenges faced by manufacturing companies today?
Manufacturing companies face HR challenges like high employee turnover, skill shortages, safety compliance, poor shift management, and low adoption of digital tools. These issues directly impact productivity, labor costs, and operational efficiency.
2. How can HR software reduce attrition and improve employee retention in manufacturing?
HR software helps reduce attrition by automating engagement surveys, tracking career development, offering shift flexibility, and implementing recognition programs—creating a more rewarding and stable workplace.
3. How does HR in manufacturing handle workforce safety and compliance?
HR plays a crucial role in managing safety protocols, conducting training, ensuring OSHA and ISO compliance, and digitizing incident reporting. A strong safety culture not only protects employees but also prevents costly legal risks.
4. What is the best way to manage shift scheduling and attendance in manufacturing?
Automated shift planning tools and mobile attendance systems help HR teams efficiently manage multi-shift operations, track working hours, reduce absenteeism, and ensure accurate payroll processing.
5. How can manufacturing HR teams close the skill gap in the workforce?
HR can bridge skill gaps by partnering with vocational institutes, launching upskilling programs, and using digital learning tools. Creating internal skill matrices and offering career progression paths also helps build future-ready teams.
6. What strategies help improve diversity and inclusion in manufacturing environments?
To boost diversity, HR can run targeted recruitment drives, set measurable D&I goals, introduce mentorship programs, and use anonymous employee feedback tools to track and improve inclusion across the factory floor.
7. Which HR platform works best for manufacturing businesses?
The ideal HR platform for manufacturing should offer modules for attendance, shift scheduling, safety tracking, payroll automation, and skills management. Solutions like peopleHum are designed to handle these sector-specific needs effectively.